Optical measuring instrument: Point auto-focus (PAI) for coordinate and surface texture measurements
Point auto-focus (PAI) optical measuring instrument works based on the principle of following the focus position of a microscope objective lens. This auto-focus mechanism follows the height of the surface of a measured object.
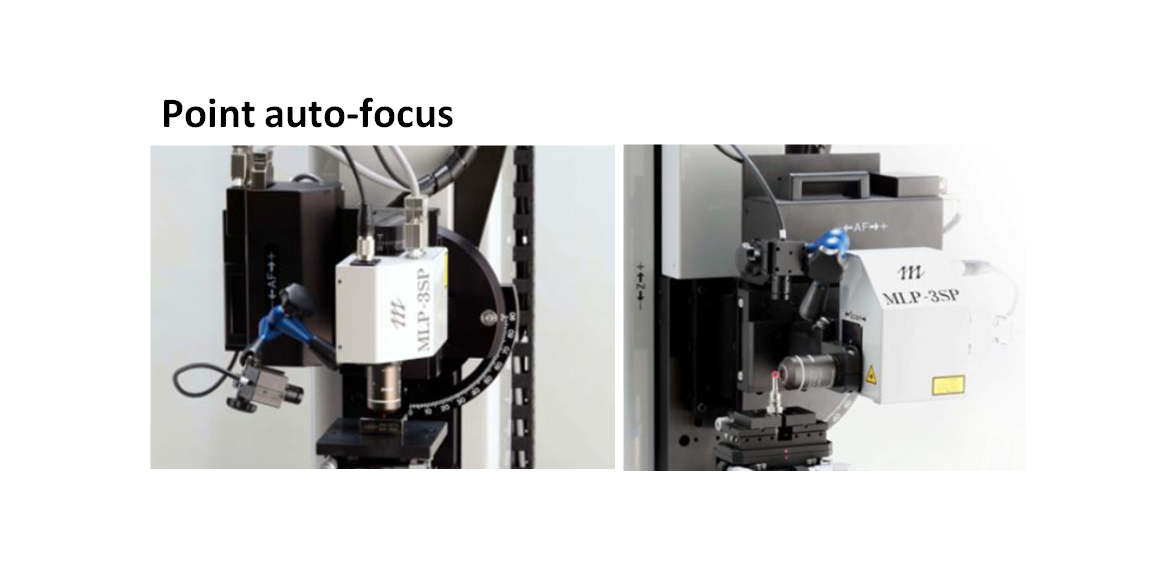
Point auto-focus (PAI) optical measuring instrument works based on the principle of following the focus position of a microscope objective lens. This auto-focus mechanism follows the height of the surface of a measured object.
That is, the other name of this instrument is “focus follower”.
When compared to a stylus instrument, that is a tactile surface measuring instrument, PAI is a stylus instrument but is based on optical (non-contact) method instead of tactile (contact) stylus.
Figure 1 below shows an example of one type of PAI instruments. This instrument is produced by a Japanese company, Mitaka Kohki. In Figure 1, Mitaka MLP-3SP is shown as one of Mitaka products based on PAI technology.
From Figure 1, MLP-3SP system consists of 4-axis linear and 1-axis rotation. The 4-axis linear system is constituted by 3-axis linear X, Y and Z motion stage and 1-axis short-distance ultra-precision axis to move the auto-focus system so that this system follow the objective lense’s focus position on a measured surface.
This 1-axis auto-focus motion system has $1 nm$ position resolution. This ultra-precise and accurate axis is used to follow the focus position of an equipped objective lens and record the focus position as the height of a measured surface.
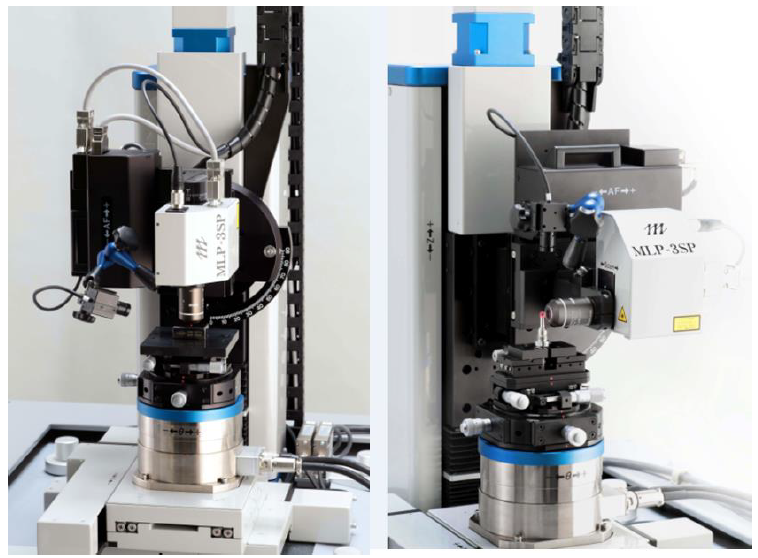
Figure 2 below presents a complete configuration of Mitaka MLP-3SP including its vibration isolation table and system enclosure. In Figure 2, the vibration isolation table is equipped with an air-floating table using an air-bearing system. The main purpose is to isolate high frequency vibration originated from ground vibration at a shopfloor or from instrument electric motors.
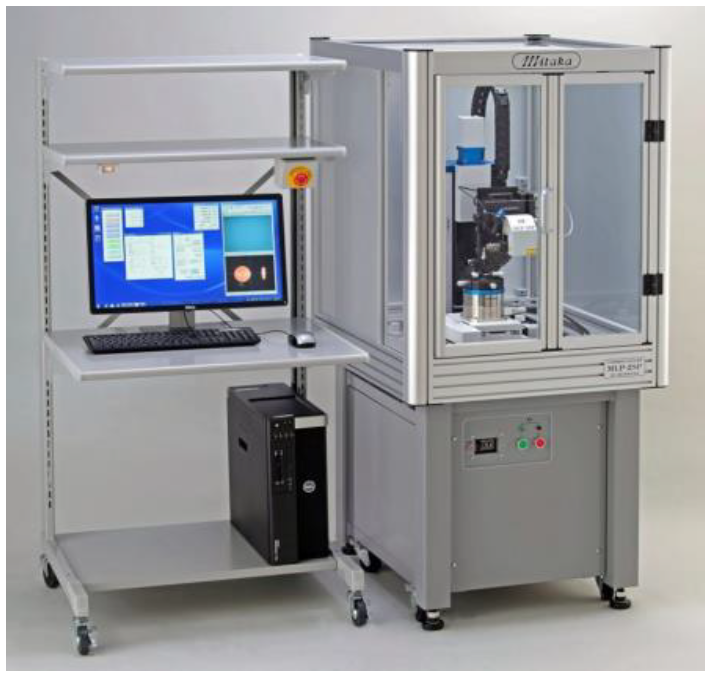
READ MORE: Digital transformation of dimensional and geometrical measurements
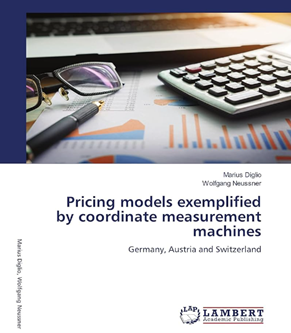
Working principle of point auto-focus measuring instrument
PAI instrument measures a surface topography by focusing a laser beam at a single point on a measured surface. On this single point, the auto-focus linear axis mechanism will automatically move the objective lens of the instrument up and down until the laser beam is at focus position of the objective lens.
When the position of the objective lens at focus, the encoder of the auto-focus linear axis and the other X,Y,Z linear axes records the objective lens position. The recorded height position of the focus position is the height of a measured surface. This process is then repeated for a complete surface profile or trajectory to finally reconstruct the entire measured surface.
The light source for PAI system is a coherent light, that is a laser. The commonly used laser is a laser with wavelength of $632 nm$, that is red laser. The size of the laser spot diameter at focus depends on the magnification and type of an objective lens used by the PAI system. With a $100\times$ objective lens, the size of laser spot diameter at focus is about $1\mu m$.
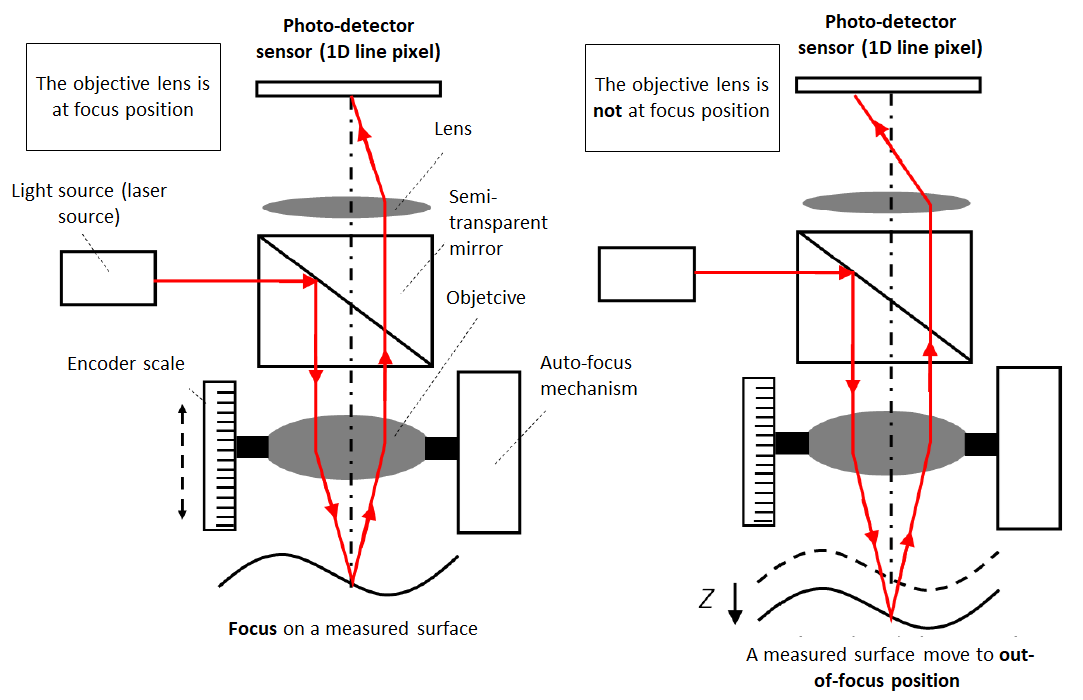
Figure 3 above shows the optical configuration and auto-focus working principle of PAI instrument. One unique aspect of PAI is that it is not equipped by a 2D imaging sensor. Instead, it is equipped by a high-sensitive auto-focus photo detector.
As mentioned before, other unique aspect of PAI is that its auto-focus linear axis has a $1 nm$ resolution so that the height of a measured surface can be detected with high accuracy.
From Figure 3 left, the laser beam of PAI system is presented at focus position at a measured surface location. When the laser is at its focus position, the location of the reflected laser beam from a measured surface will be towards the centre point of the auto-focus photo-detector sensor.
Meanwhile from Figure 3 right, the laser beam position is out-of-focus so that the reflected laser beam will be at non-centre location of the auto-focus photo detector system. Due to this non-centre location at the auto-focus sensor, the auto-focus linear motion system will move the objective lens up and down until the reflected laser beam falls at the centre of the auto-focus system, that is the objective lens is at its focus position.
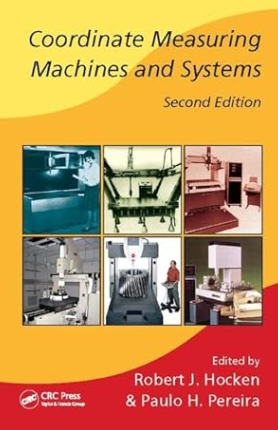
Application of point auto-focus optical measuring instrument
Applications of PAI measurements are vast. PAI instrument can be used for dimensional, geometrical and surface texture measurements.
Figure 4 below shows some examples of PAI measurement capabilities. In Figure 4a, a cylindrical part is measured by a PAI system. The part is a shaft with some slot features as mating feature to its counterpart. The measurement is a geometrical measurement of the diameter of the part.
READ MORE: Understanding fundamental assembly features: Mate and contact features
Figure 4b and 4c shows examples of internal and external diameter of sphere with micrometre size. Figure 4d and 4e shows surface texture measurements of nano indentation part and an animal tooth, respectively.
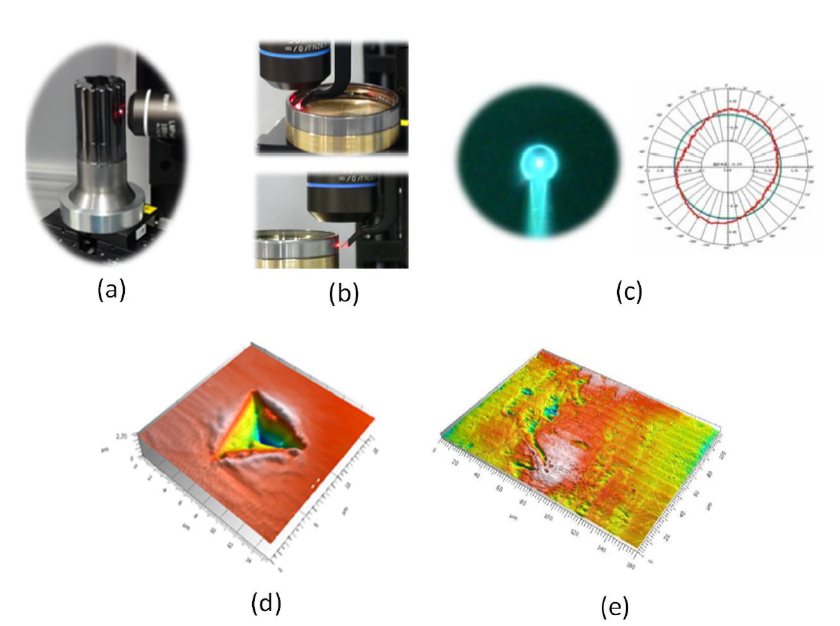
Advantages of a point auto-focus system
- PAI can be used for all types of measurements: dimensional, geometrical and surface texture measurements.
- PAI has a relatively large measuring volume, such as $(120\times 120\times 130)$ mm depending on the type.
- The range of the high-resolution auto-focus linear axis can reach up to 40 mm. that is, it can measure parts with surface height variation up to 40 mm, this is large!
- The 2D profile or contour measurement is fast
- PAI can measure a surface with high surface slope. PAI can measure a slope up to 45 degree with $100\times$ objective lens with numerical aperture (NA) =0.8
- PAI has a very high auto-focus repeatability at around 15 nm.
- PAI can measure various types of surfaces including very reflective surfaces
- PAI has various types of configurations to measure various complex and uncommon geometry, such as internal feature measurements.
Some drawbacks of a point auto-focus system
- 3D areal surface texture measurement will be relatively slow because a PAI system need to measure a surface profile-by-profile (section-by-section) but with high accuracy from various surface material including reflective surface
- The slope measurement capability will be reduced for a very high reflective surface
- Depending on PAI instrument configurations, the selection of objective lens could be limited
READ MORE: Optical coordinate measuring machine (Optical-CMM): Two fundamental limitations
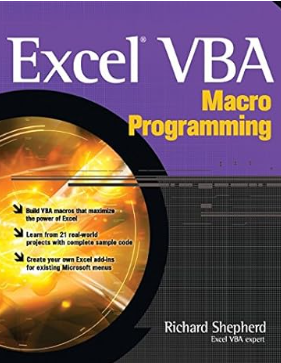
Conclusion
In this post, one of optical measuring instrument, that not many people have known, has been presented and discussed, that is Point auto-focus optical measuring instrument.
This instrument is manufactured and commercialised by Mitaka Kohki, Japan. Not many manufacturers commercialise optical measuring instrument based on point auto-focus.
The instrument has a wide variety of measuring applications, covering dimensional, geometrical and surface texture measurements. Not many optical instruments can cover both geometrical and surface texture measurement at the same instrument.
The advantages of this instrument have been presented along with some drawbacks (remember, there is not a single instrument that can do it all without any drawbacks). However, the drawbacks do not reduce the high benefits the instrument can provide for measurements in manufacturing, laboratory and other fields.
You may find some interesting items by shopping here.
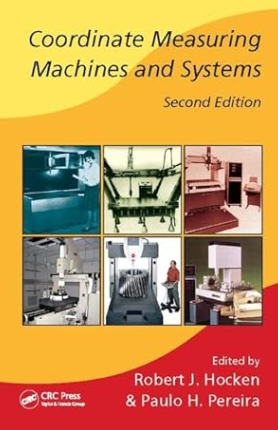